Die Cast Mold | Zinc Die Casting Tooling
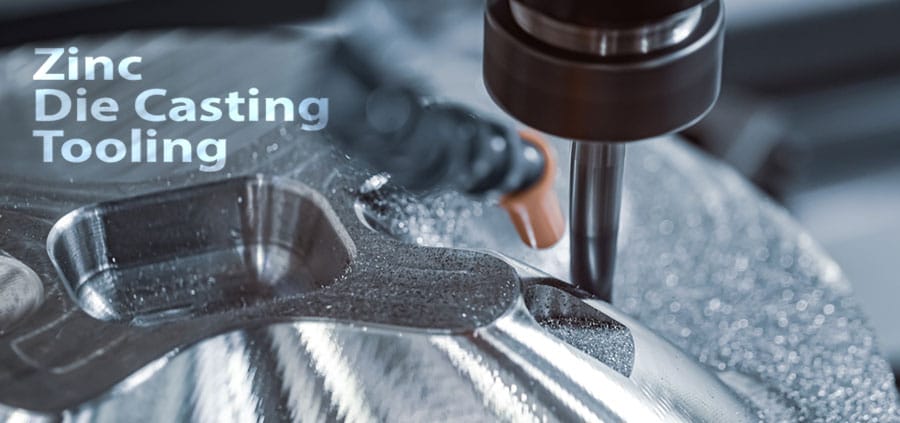
In the zinc die casting process, tooling for die casting plays the fundamental role. Die casting dies, or mold ensure efficiency, precision, and cost-effectiveness in creating die cast parts. The choice of zinc die casting tooling, whether it’s a single die cavity or multi-cavity mold, may impact production speed, part quality, and overall costs. Below is a breakdown of different tooling types used in zinc die casting and tips on how to choose the right option.
Introduction to Zinc Die Casting Tooling
Die cast tooling typically refers to the die or mold cavity used to shape molten metal into net-shape parts. Although “Tooling” may refer to additional components, like ejector pins, slides, and cooling channels. When discussing tooling with customers, the mold is often the primary component referenced.
Mold: The hollow form used to shape molten zinc into repeatable consistent net-shape zinc castings. Mold flow simulation software, such as Flow3D-Cast, helps Design Engineers to anticipate mold performance in the design stage.
Tool: Made from high strength steel and consists of two parts or halves of the mold. The two halves run in a die casting machine during the production process.
Die: In manufacturing the term die and mold are interchangeable. As both describe the tool in which molten metal is injected under high pressure die casting.
Engineers design these tooling systems to handle the rigors of the zinc die casting process. This process injects molten metal into molds at high pressure. The quality and durability of these tools directly impact the performance and lifespan of the final cast parts.
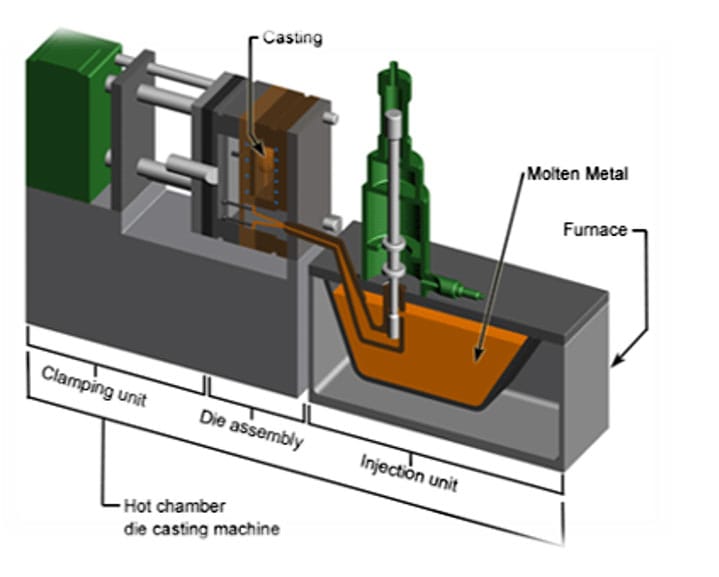
In Hot Chamber die casting, there is a pot of molten metal that the machine uses to inject the metal into the mold. Zinc alloys with low melting temperature, typically use this process.
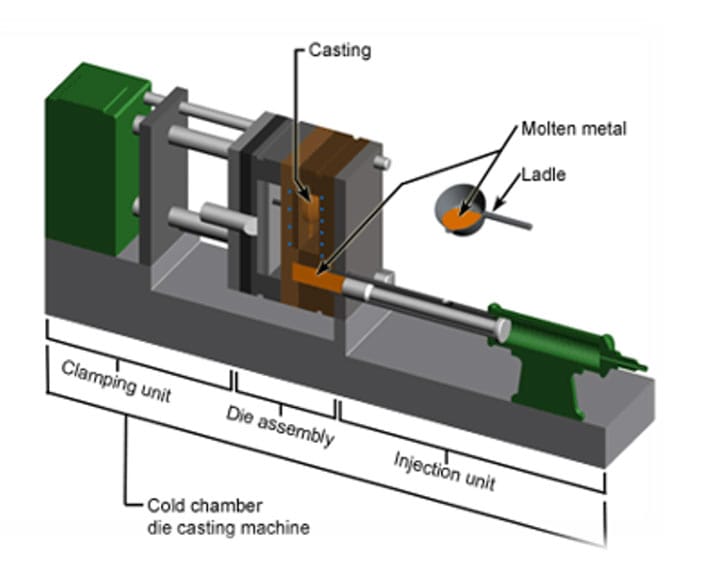
In Cold Chamber die casting, a ladle adds molten metal into the machine before each shot. Preparing it for injection into the mold. This process is typically for alloys with high melting temperatures, such as aluminum die casting.
Types of Die Casting Tooling
Self-contained Molds are a complete mold base and holder. They have a higher tooling cost, may contain multiple slides on all side and have a center sprue.
Unit Molds are the industry standard and have a lower tooling cost. The die casting companies own the holder. A customer typically will own the unit die. Unit dies limit slide locations.
Multi-slide Mold
Most conventional dies have two halves that form the cavity shape of the part that will be formed during the casting process. However, Mult-slide mold allow manufacturers to form the mold from more than two pieces. This design allows the casting of more complex shapes than a conventional two-half tool can produce.
Understanding Cavities
Single Cavity Mold
A single cavity molds produce one part per cycle or shot. These molds are suitable for producing thin-wall parts or highly intricate casted parts in low-volume runs.
Multi-Cavity Mold
Multi-cavity molds contain multiple cavities that allow for the production of several parts in one cycle. They are ideal for making high-volume production where speed and consistency are crucial. Multi-cavity molds are highly efficient for large-scale manufacturing.
Family Mold
Family molds can produce different components simultaneously in a single mold. Which is particularly useful when creating parts for a product assembly.
Group Molds
Group molds can be used to run different components using shared mold components. This will most commonly occur when parts have some features which are identical, and only vary on a few features.
As an example, a broom-tip that is identical but has two different lengths. You can produce it using the same tool with a different insert or core to create the other part. Group molds share much of the tooling allowing for reduced tooling cost.
Choosing the Right Tooling for Your Needs
Production Volume
For high volume parts, it is typically best for each part to run in its own tool. However, in small production runs or parts that have the same usage a family tool is a consideration.
Part Complexity
Complex geometries or designs with thin walls may require specialized zinc die casting tooling. Such as single cavity molds, for high quality casting. Multi-cavity molds may be more suitable for simple, high-volume parts.
Precise Needs
Some customers need parts with low variations on key dimensions. These variance requirements will have implications on the manufacturing process. Both on how the part is designed in the tool and how many cavities should be used. As more cavities create an additional source of subtle potential variance from part to part.
Lead Time
When a group mold is developed, the parts that share that mold cannot be run at the same time. Unfortunately, this means that the average lead-times will get longer as one part has to be produced in sequence rather than in parallel. This limitation can easily be worked around through proper planning, but it is important to remember that it creates a tooling constraint.
Budget Considerations
Some tooling can be designed to minimize the upfront cost but may come with consequences of higher production costs or shorter tool life. It is important to always remember that there will be tradeoffs when committing to a tooling decision.
Conclusion
Zinc die casting tooling is essential for efficient, cost-effective production. By knowing the differences between single cavity, multi-cavity, and family molds, manufacturers can make better choices. They should think about part complexity, volume, and budget; this way, they can select the best tooling for their needs.
There are always tradeoffs when making these decisions, so it is helpful to have an in-depth conversation with an Engineer to validate that the tooling plan will help you balance your total cost over the lifespan of the product.
Many Thanks to Deco Products, Feel free to reach out to the zinc die casting experts at Deco Products to discuss your die cast tooling project.
DECO PRODUCTS DESIGN & ENGINEERING
DECO PRODUCTS Website:
www.decoprod.comAuthor: Michele Duwe, Marketing Deco Products
Michele is an experienced technical writer and marketing expert with years in writing articles in the manufacturing industry.