Precision Under Pressure: How Aerospace Sheet Metal Fabrication Supports Mission-Critical Demands
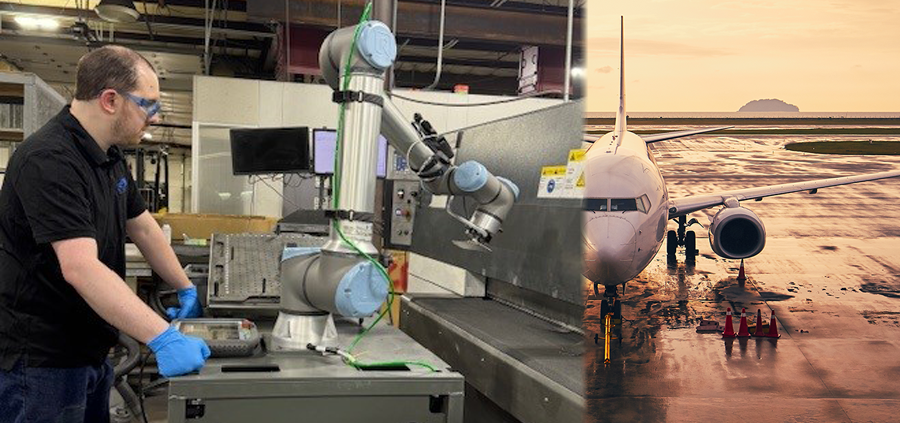
In aerospace and defense, precision isn't just desirable — it's non-negotiable. That's why aerospace sheet metal fabrication plays a central role in delivering reliable, high-performance components for mission-critical applications. From structural elements to shielding and enclosures, fabricated sheet metal parts form the backbone of countless systems used in air and space platforms.
Aerospace engineers and supply chain professionals know the challenges well: high-vibration environments, extreme temperatures, weight restrictions, and rigorous regulatory requirements. Fabricated metal components must stand up to these conditions while meeting tight tolerances and remaining cost-effective. Success depends on understanding the materials, processes, and compliance frameworks that drive this demanding field.
Material Selection for Aerospace Environments
The choice of material is a defining factor in aerospace sheet metal fabrication. Lightweight and strong alloys like 6061 or 5052 aluminums are common, offering excellent strength-to-weight ratios and corrosion resistance. For higher-temperature or more corrosive environments, titanium and certain stainless steels may be preferred despite higher costs or fabrication complexity.
Each material presents unique forming and joining challenges. For instance, titanium offers exceptional strength but requires careful heat control during welding. Understanding how different materials respond to fabrication processes is key to preventing warping, cracking, or premature fatigue.
Advanced Fabrication Techniques
Meeting aerospace standards means employing precision technologies. CNC turret punching, laser cutting, and automated press brake forming are standard tools in the aerospace fabricator’s toolbox. These allow for exacting dimensional control, fast prototyping, and consistent repeatability across production runs.
Automation is also critical. The use of robotics improves consistency and reduces human error. Computer-aided design (CAD) and manufacturing (CAM) systems enable engineers to simulate part fabrication before materials are even touched, improving efficiency and reducing rework.
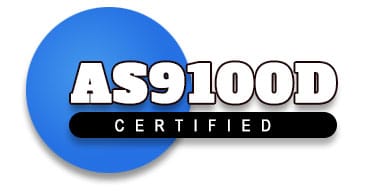
Navigating Certification and Compliance
AS9100 certification is more than a badge — it's a necessity for working with aerospace clients. It ensures that a fabricator adheres to rigorous quality management systems, documentation practices, and process controls. Engineers and sourcing professionals should seek fabrication partners who can offer full traceability, from raw materials to finished parts.
Documentation and inspection requirements often include:
- Material certificates
- First article inspections (FAI)
- In-process and final inspections
- Detailed process documentation for traceability
Adherence to these standards not only ensures regulatory compliance but also streamline audits and reduces the risk of production delays.
Design for Manufacturability in Aerospace
Complex part geometries and tight packaging constraints are common in aerospace systems. Early collaboration between design engineers and fabrication teams helps avoid costly design revisions. Key considerations include:
- Reducing the number of separate parts by combining features
- Designing with standard bend radii and material thicknesses in mind
- Simplifying assemblies for faster production and maintenance
Understanding these principles allows engineering teams to create designs that are both functional and efficient to manufacture.
Looking Ahead
The future of aerospace sheet metal fabrication lies in continued innovation. New materials, additive-manufacturing hybrids, and digital thread technologies promise even greater precision, traceability, and agility. However, the fundamentals remain the same: success in aerospace fabrication requires deep expertise in materials, tight process control, and a proactive approach to compliance.
For sourcing and engineering teams, staying informed about fabrication best practices is essential to building reliable supply chains and delivering high-quality products on time.
One example is Geater Machining & Manufacturing Company, located in Independence, Iowa. Their sheet metal expertise supports high-tech and aerospace clients through process knowledge, quality-driven practices, and a strong understanding of regulatory compliance. New materials, additive-manufacturing hybrids, and digital thread technologies promise even greater precision, traceability, and agility.
For sourcing and engineering teams, staying informed about fabrication best practices is essential to building reliable supply chains and delivering high-quality products on time.
Many thanks to Geater Machining and Manufacturing Company for their input to our article.