The Future of Manufacturing: Trends to Watch
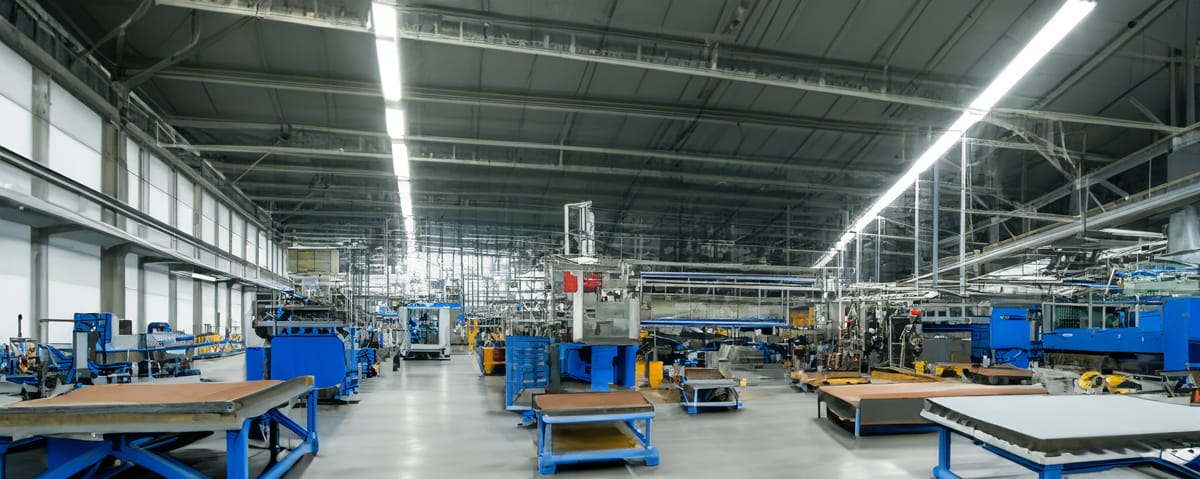
Today, the manufacturing sector stands on the brink of a transformative era, driven by rapid technological advancements and shifting global dynamics. For professionals navigating this complex landscape the ability to stay informed about emerging trends is not just advantageous; it's imperative. This article aims to shed light on the most significant trends and changes in the manufacturing industry, offering insights into why they matter and how they could impact the future of your operations. Understanding these trends is crucial for staying competitive, driving improvement, and making informed decisions in a rapidly evolving market.
Automation and Robotics
Robotic Process Automation (RPA) is changing the way mundane and repetitive tasks are performed. By delegating these tasks to robots, manufacturers can free up their human workforce to focus on more complex and creative problem-solving tasks, thereby increasing productivity and job satisfaction.
Collaborative Robots (Cobots) are another game-changer. Designed to work alongside humans, cobots are equipped with sensors and AI to ensure safety and adaptability in shared workspaces. Their versatility and ease of programming make them suitable for a wide range of applications, from assembly lines to quality control, making them invaluable assets for manufacturers looking to boost efficiency without compromising on safety.
The integration of Advanced Robotics into manufacturing not only streamlines production but also significantly reduces operational costs. Robots are capable of operating 24/7, reducing downtime and increasing output. Moreover, they can perform tasks with a level of precision and consistency unmatched by human labor, leading to improvements in product quality and a reduction in waste.
However, the rise of automation and robotics also presents challenges, particularly in terms of workforce development and the skills gap. As the demand for technical skills increases, manufacturers must invest in training and development programs to ensure their workforce can effectively collaborate with these new robotic counterparts.
Artificial Intelligence and Machine Learning
Artificial Intelligence (AI) and Machine Learning (ML) are not just buzzwords but pivotal technologies driving significant advancements. The integration of AI and ML into manufacturing processes is setting new benchmarks for efficiency, innovation, and quality.
Predictive Maintenance is one of the most impactful applications of AI and ML in manufacturing. By analyzing data from equipment sensors, AI algorithms can predict failures before they occur, minimizing downtime and maintenance costs. This proactive approach ensures that operations run smoothly and efficiently, with the added benefit of extending the lifespan of machinery.
Quality Control has been revolutionized by AI's ability to analyze vast amounts of data quickly and accurately. Machine learning models, trained on datasets of product images or performance metrics, can identify defects or anomalies faster and more reliably than human inspectors. This not only improves product quality but also reduces waste and enhances customer satisfaction.
Supply Chain Optimization is another area where AI and ML are making a significant impact. By analyzing trends and patterns in supply chain data, AI can forecast demand, optimize inventory levels, and identify potential disruptions. This enables manufacturers to make informed decisions, reduce costs, and improve supply chain resilience.
Customization and Design benefit from AI's ability to process and analyze customer preferences and feedback. Manufacturers can use this data to design and produce highly customized products, meeting specific customer needs and opening up new market opportunities.
The adoption of AI and ML in manufacturing also poses challenges, particularly in terms of data privacy, security, and the ethical use of AI. Manufacturers must navigate these challenges carefully, ensuring that they use AI responsibly and transparently. For professionals in the field, staying abreast of these technologies and understanding how to leverage them is crucial for growing their business in a changing world.
Additive Manufacturing
The area of additive manufacturing, more commonly known as 3D printing, is not just an emerging technology but a fundamental shift in the production paradigm. This method of manufacturing, which builds objects layer by layer from digital models, is transforming industries by offering unprecedented flexibility, efficiency, and customization.
Rapid Prototyping is one of the most immediate benefits of 3D printing, allowing designers and engineers to quickly turn concepts into functional prototypes. This accelerates the design process, enabling faster iterations and innovation. The ability to rapidly prototype also significantly reduces the time and cost associated with traditional manufacturing methods.
Supply Chain Simplification is another significant advantage. Additive manufacturing allows for the production of parts on demand, reducing the need for large inventories and minimizing supply chain complexities. This not only cuts down on storage and logistics costs but also enhances the ability to respond quickly to market changes or disruptions.
Despite its advantages, the adoption of 3D printing also presents challenges, including the need for skilled operators, concerns about intellectual property, and the limitations of materials suitable for additive manufacturing. However, ongoing advancements in technology and materials science are rapidly addressing these issues, broadening the applications and accessibility of 3D printing.
The Internet of Things (IoT) and Smart Factories
The Internet of Things (IoT) is fundamentally transforming the manufacturing landscape, ushering in the era of smart factories. These interconnected environments use IoT devices to collect, analyze, and act upon data in real-time, driving efficiency, productivity, and operational excellence.
Real-Time Monitoring and Analytics are at the heart of smart factories. IoT sensors and devices continuously gather data from equipment and processes, providing a comprehensive view of operations. This real-time insight enables manufacturers to identify inefficiencies, predict potential issues before they arise, and optimize production processes, leading to significant cost savings and improved product quality.
Energy Management and Sustainability efforts are bolstered by smart factory technologies. IoT devices monitor and control energy usage across operations, identifying opportunities for savings and reducing the environmental footprint. This aligns with growing regulatory and consumer demands for sustainable manufacturing practices.
Enhanced Safety and Security measures are made possible through the IoT. Sensors can detect hazardous conditions, equipment malfunctions, or unauthorized access, triggering alerts and enabling swift action to protect workers and assets.
IoT and smart factories represent a great leap forward in manufacturing technology, offering the potential to revolutionize every aspect of production. For professionals in the field, embracing these technologies is essential for enhancing operational efficiency, sustainability, and competitiveness in a rapidly evolving global market. As we continue to innovate and integrate IoT solutions, the future of manufacturing looks increasingly connected, intelligent, and sustainable.
Author Biography:
Neal Rabogliatti has over 30 years in the manufacturing sector working with a wide range of companies in marketing and promotion as well as helping companies strategically promote new technology as a part of their value proposition and a way to stand out against their competitors.