Thin Wall Die Casting in Zinc Alloys
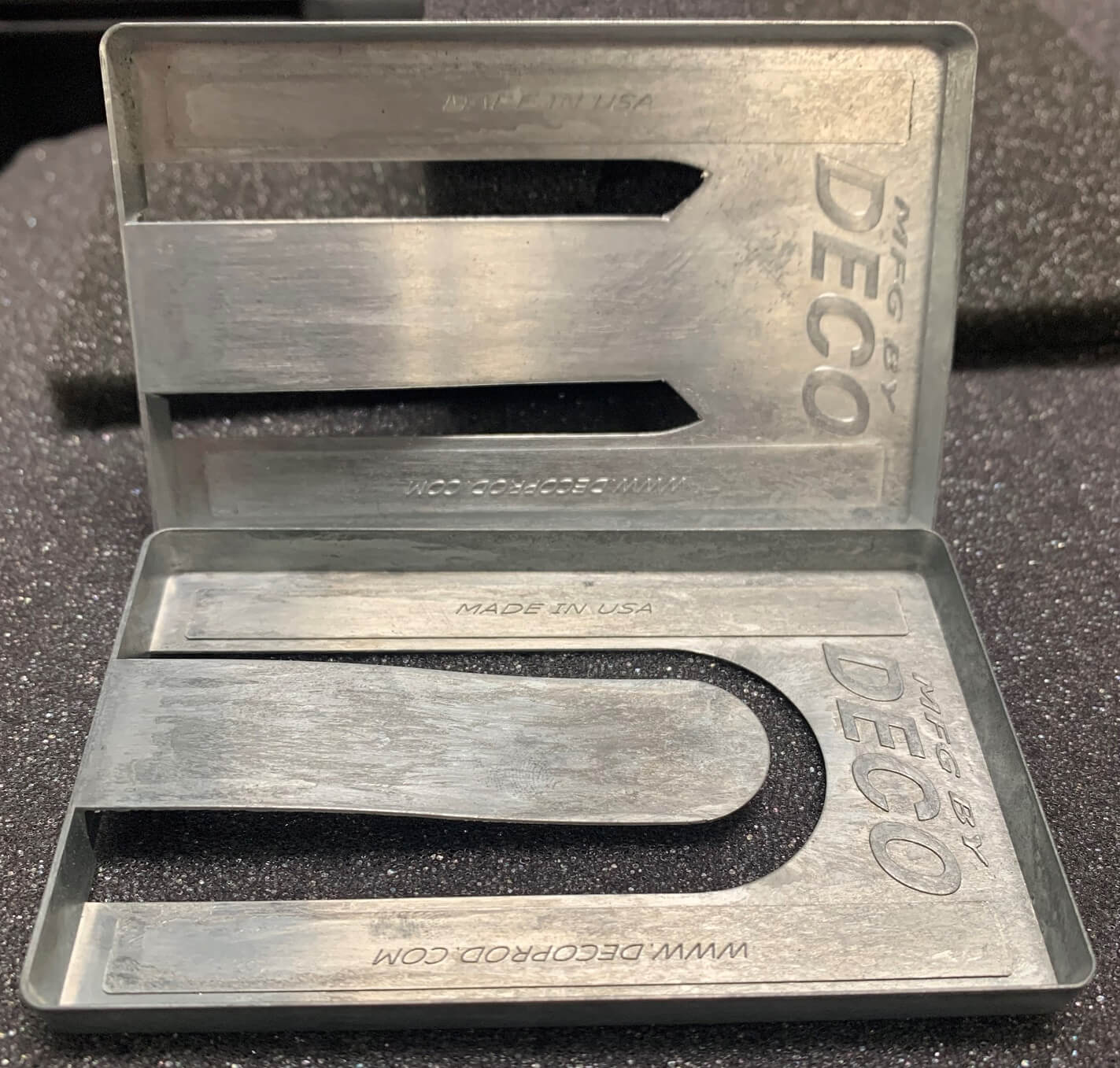
Thin wall zinc die casting is the process of creating complex, lightweight metal components using a high-pressure injection molding technique. This innovative manufacturing process allows for the creation of intricate, precision engineered components with remarkable dimensional stability and strength.
By utilizing thin wall zinc die casting, manufacturers can produce lightweight, high-performance components with excellent surface finishes. Making them ideal for a wide range of industrial and consumer applications
What are the advantages of thin wall thickness in zinc die cast?
Zinc die casting with thin wall thickness offers several advantages, including:
· Reduced Material Costs: Less material is required, resulting in reduced production costs.
· Lighter Weight: Components are lighter in weight, which is ideal for weight reduction in critical applications.
· Enhanced Performance: Thin walls can improve the strength and durability of components, allowing for better performance and complex designs.
· Faster Cycle Times: Components cool more quickly, allowing for faster production cycle times.
· Increased Design Flexibility: Components with smoother surface finishes and intricate detail, resulting in a more polished appearance.
Overall, the advantages of thin wall thickness in zinc die casting allow for greater design flexibility, cost effectiveness, and improved performance. Making it a preferred choice for a wide range of industrial and consumer applications.
Design Considerations for die casting process
Design considerations are crucial for the successful production of thin wall zinc die casting components. The following are some important design considerations to keep in mind:
Wall Thickness
One of the most critical design considerations for thin wall zinc die casting is wall thickness.
Wall thickness impacts the structural integrity of the component and can affect the part’s ability to fill the mold properly. Walls that are too thin can result in porosity or the formation of voids.
On the other hand, walls that are too thick can increase the weight of the component, leading to increased costs and reduced performance. It's important to balance wall thickness with the component's requirements to ensure the best performance and cost-effectiveness.
Draft Angles
Draft angles refer to the taper on the vertical surfaces of a component. Draft angles are essential to ensure that the component can be ejected from the mold easily.
A lack of draft angles can lead to components getting stuck in the mold, causing damage and costly downtime. The recommended draft angles typically range between 0.5 to 1 degree, depending on the component geometry.
Radii and Fillets
Sharp edges and corners can cause stress concentration in components, leading to cracks and failure over time. Therefore, it's important to use radii or fillets to smoothen corners and reduce stress concentration.
In addition, radii and fillets can help improve the flow of molten metal during the casting process.
Parting Lines
Parting lines refer to the point where the two halves of the mold meet. These lines can be visible on the final component and affect the appearance and surface finish of the component.
Designers should consider the placement of parting lines carefully to minimize their impact on the final component's appearance and performance.
Zinc Die Casting: A Wise Decision
Overall, zinc is an excellent choice for die casting projects due to its strength, precision, surface finish, cost-effectiveness, and environmental sustainability. By utilizing zinc die casting, manufacturers can produce high-quality components that meet the requirements of a wide range of industries, including automotive, electronics, and consumer goods.
We cordially invite you to explore the benefits of Zinc Die Casting and how it can enhance your manufacturing process. To learn more please visit the website below.
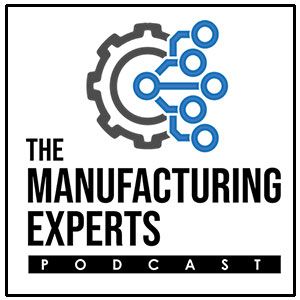
DECO Products - https://decoprod.com/
Author: Michele Duwe